Blind Flange is a key pipe fitting used to seal and isolate pipeline sections in various industries. As engineering requirements for safety, maintenance, and durability intensify, the correct selection of blind flange types is crucial for reliable industrial operations.
Product Intro: Blind Flange
Main Keywords: blind flange types, blind flanges types, types of blind flange
1. Industry Development Trends: Blind Flange Types in Global Markets
-
Growth Rate:
According to MarketsandMarkets, the global industrial flange market, including blind flange types, is expected to reach USD 6.2 billion by 2028, with a CAGR of 4.8% (2022–2028).
-
Key Sectors:
Oil & Gas, Chemical/Petrochemical, Power Generation, Metallurgy, Wastewater Treatment are major consumers of diverse blind flanges types.
-
Certification Trends:
Demand for ISO 9001, ASME B16.5, ANSI, EN 1092–1 certified blind flange types is rising across Europe, North America, and emerging Asian markets.
-
Material Shifts:
High-performance alloys, duplex stainless steel, and corrosion-resistant coatings (PTFE, FBE) are gaining share for critical pipeline applications.
-
Digital Manufacturing:
Integration of CNC machining, ultrasonic flaw detection, and 3D measurement enhances precision and longevity for various types of blind flange.
2. Overview: Classification & Technical Comparison of Blind Flange Types
Blind flanges (also known as blanking flanges or end flanges) are used to close the end of pressure vessel nozzles or piping systems, permitting inspection, pressure testing, maintenance, or future pipeline expansion. Selecting the right blind flange type depends on:
- Piping pressure/class rating
- Material compatibility & corrosion requirements
- Connection standard (e.g., ANSI, DIN, JIS)
- Site-specific customization (raised face, RTJ grooves, special coatings)
Blind Flange Types: Key Parameters Comparison Table
Type |
Standard |
Material Options |
Pressure Class |
Sealing Face |
Typical Size Range |
Industry Use |
Flat Face (FF) |
ANSI, ASME B16.5 |
CS, SS, Alloy Steel |
150-600 |
Flat |
1/2”–48” |
Water, HVAC, Low Pressure |
Raised Face (RF) |
ANSI, ASME, DIN |
SS, CS, Duplex |
150–2500 |
Raised |
1/2”–48” |
Oil & Gas, Marine |
Ring Type Joint (RTJ) |
ANSI, API, DIN |
F51, F11, A105, Inconel |
300–2500 |
Grooved |
2”–24” |
High/Ultra Pressure |
Forged Blind |
ASME, JIS |
Forged Steel, SS316 |
150–1500 |
RF, RTJ |
1/2”–60” |
Power, Chemical |
Threaded Blind |
ANSI B16.5 |
CS, Alloy |
150–600 |
Threaded |
1/2”–12” |
Process, Instrumentation |
Custom Blind (with Nozzle, Vent, NPT tap) |
ASME B16.47, Customized |
All |
Any |
Customized |
1/2”–120” |
Specialty, OEM Projects |
3. Blind Flange Types Manufacturing Process Detail (with Flowchart)
Process Flow Summary:
-
Raw Material Selection: High-grade carbon steel, stainless steel, alloy or duplex steel billets ensuring required mechanical and anti-corrosive properties. Compliant with ASTM, JIS, EN standards.
-
Forging/Casting: Billets are forged under high pressure (hydraulic presses; 1,000–4,000 tons) or cast in controlled environments to shape basic flange bodies.
-
Heat Treatment: Homogenize grain structure by normalizing, quenching, tempering for optimum strength/ductility. Strict temperature & time control (ASME/ASTM).
-
CNC Machining: Precision turning, facing, grooving (RTJ or spiral serration), and boring to configure sealing faces and bolt holes, tolerance ±0.02 mm.
-
Surface Finishing: Shot blasting, anti-corrosive coating (FBE, galvanized, PTFE). Stamping of standards, pressure class, batch no.
-
Testing/Inspection: Dimensional, visual and third-party NDE (Ultrasonic, Magnetic Particle, Hydrotest) as per ISO 9001, API 6A, EN 10204 3.1/3.2.
-
Packing & Delivery: Secure wooden case/ply-box packing with mill reports, certificates.
Blind Flange Types: Manufacturing Flowchart
Material Selection
➜
Forging/Casting
➜
Heat Treatment
➜
CNC Machining
➜
Surface Finish
➜
Inspection & Test
➜
Packing & Shipping
ISO 9001, ASME B16.5, API 6A Compliance at Each Stage
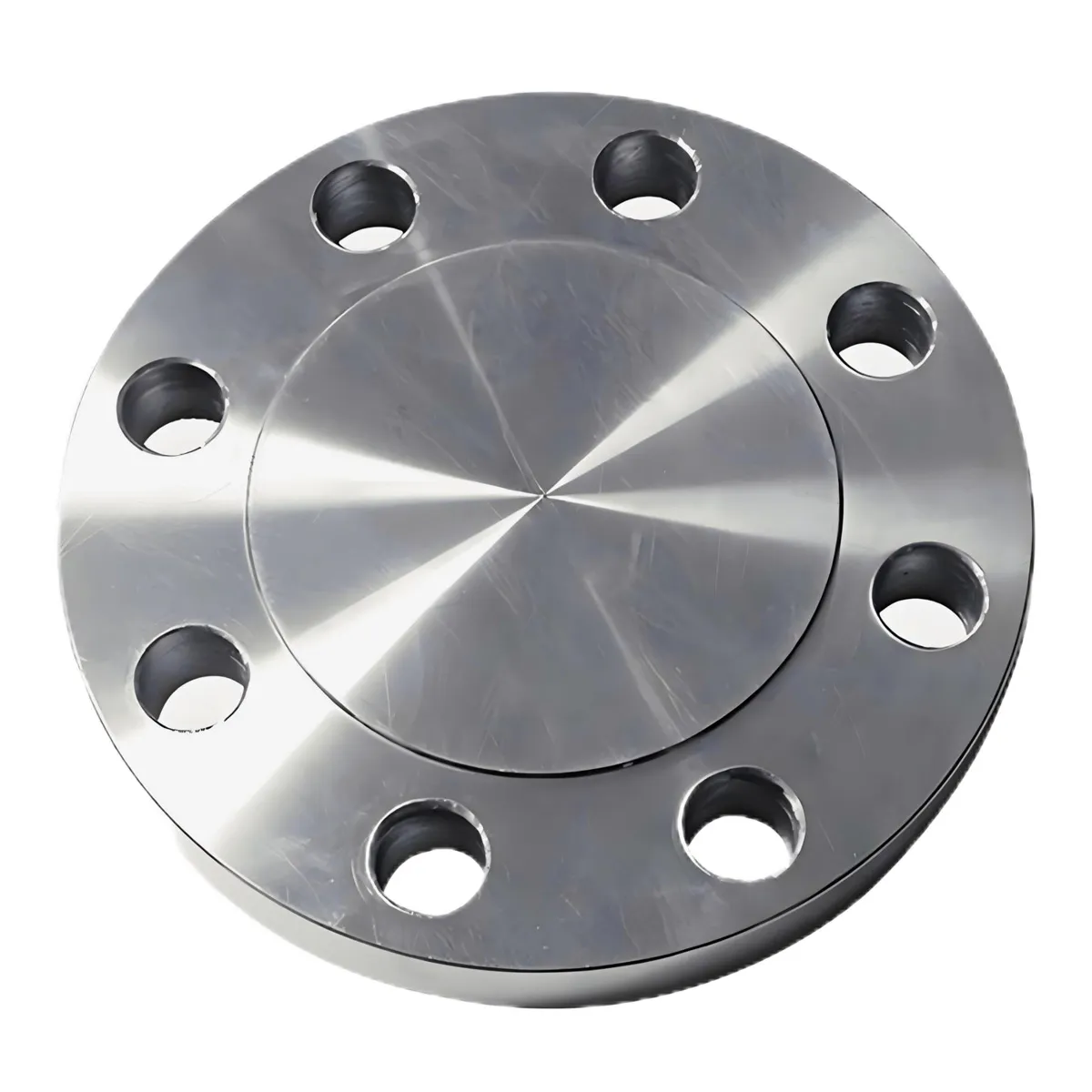
4. Key Technical Parameters for Blind Flange Types
- Available Sizes: 1/2"–120" (12–3,000 mm) as per blind flange types standard
- Pressure Ratings: Class 150, 300, 600, 900, 1500, 2500 per ASME/ANSI B16.5/B16.47
- Temperature Range: −70°C to +600°C (depending on material and gasket type)
- Seal Face Types: FF, RF, RTJ, Groove or custom
- Coating Options: Black oxide, Hot dip galvanized, FBE, PTFE
- Hardness: HB 120–235 typical for CS/SS
- Life Expectancy: > 25 years for quality-certified products
- Leak Rate: <10−5 mbar.l/s in pressure sealing applications
5. Major Manufacturers: Quality/Price & Customization Comparison
Blind Flange Types Leading Manufacturers Comparison
Company |
Regions |
Certifications |
Main Materials |
Standard Range |
Custom Services |
Price Level |
Warranty |
HBJY Pipeline (link) |
Global (APAC, EU, NA) |
ISO, PED, CE, API 6A |
CS, SS, Alloy, Duplex, Nickel |
B16.5, B16.47, JIS, DIN, EN1092 |
OEM logo, Special coatings, Large-size |
$$ |
5–10 yrs |
Bonney Forge |
USA, EU |
ASME, PED |
CS, SS |
B16.5, B16.47 |
Custom machining, RTJ grooves |
$$$ |
5 yrs |
Metalfar |
Italy, India |
ISO, EN, PED |
CS, SS, Alloy |
EN1092, DIN |
Extra-thick, Modified bore |
$$$$ |
3–5 yrs |
Shanxi Yubo |
China, Asia |
API, ISO |
CS, Alloy |
ANSI, JIS |
Drilled, Vent, Large-diameter |
$ |
3 yrs |
6. Custom Blind Flange Types Solutions & Engineering Services
- Design Services: Provide drawings and 3D models (SolidWorks/AutoCAD) based on site specs/applications.
- Material Selection: Engineering consultancy for corrosion, abrasion, and pressure criteria (Duplex, Monel, Inconel on request).
- Custom Machining: Special face finish (serrated, phonographic), custom thickness, special drilling, NPT/BSP tapping, integral nozzle/vent/drain.
- Third-Party Certificates: EN 10204 3.2, SGS, Lloyd’s, DNV-GL for projects.
- Fast Prototyping: CNC rapid proto within 1–7 days for urgent project shutdown or EPC packages.
- Coatings: FBE, Teflon, or high-temperature industrial paints to customer specification.
- Packaging: IPPC-marked, seaworthy export cases with batch traceability and laser-marked codes.
Sample Engineering Case: Power Plant Flue Gas Desulfurization (FGD)
In a recent retrofit at a 2×660 MW supercritical power station, a leading EPC utilized RTJ blind flange types (Class 900#) in their wet FGD absorber loop.
Highlights:
✔ Material: Duplex 2205 to resist high chloride & acid condensate
✔ Seal Face: Serrated finish for gasket bonding; NDE AT100% (EN10204 3.2)
✔ Result: Improved uptime, zero leakage over 3-year operation, maintained under design pressure (12.5 MPa, T≤143°C).
7. Application Scenarios: Blind Flange Types in Industry
-
Oil & Gas Refining:
For block/blind isolation, facilitating online maintenance (hot work) and ensuring worker safety during turnarounds. Raised Face and RTJ blind flange types preferred for Class 600–2500 pressure controls.
-
Pulp & Paper:
Applied in corrosive chemical tanks and bleach plant piping, with lined or alloy-coating options to prevent equipment failure.
-
Petrochemical Process:
Used in process section isolation, and for periodic pressure/vacuum testing of vessels, per API/ASME codes.
-
Water & Power Industry:
Large-diameter flanges (up to 120”) for stack, absorber and condenser circuits, especially where "nozzle" customizations are required for instrumentation access.
-
Marine/Shipbuilding:
For seawater, ballast piping—requiring anti-rust and marine-certified coatings. Threaded blind flanges types used for easy replacing.
-
Metallurgy/Mineral:
Forged and overlay blind flange types in abrasive slurry and dust-laden pipelines.
-
Pharmaceutical & Clean Room:
Pharmacopeia/FDA-compliant materials (SS316L, electropolished) with silicone/PTFE gaskets for hygienic isolation.
Advantages of Premium Blind Flange Types
- Tight Seal: Zero visible leakage (−5 mbar.l/s with correct gasket, per EN1779).
- Long Service Life: 25–35 years in typical environments for ISO/ASME products.
- Customization: Large OD, special tapping, submerged venting, multi-standard drilling on demand.
- Corrosion Resistance: Coatings and material upgrades for aggressive media (e.g., H2SO4).
- Certification Traceability: Full MTC, PMI, and NACE test reports provided.
8. Expert FAQ: Blind Flange Types - Technical FAQs
Q1. What are the material options for blind flange types?
Common choices include Carbon Steel (A105, A350), Stainless Steel (304, 316L, 321), Alloy Steel (F11, F22), Duplex Steel (2205, 2507), Nickel Alloys (Inconel 625/825, Monel 400), and occasionally non-ferrous grades for specific chemical resistance.
Q2. What standards do blind flange types comply with?
Typical blind flanges follow ASME B16.5, ASME B16.47 Series A/B, API 6A & 6B, EN 1092–1/2, and JIS B2220, depending on application and region.
Q3. How do you select sealing face for different types of blind flange?
The most common are Raised Face (RF) for high pressure, Flat Face (FF) for low/medium pressure, and RTJ (Ring Type Joint) for extremely high-pressure, high-leak tightness requirements. Choice depends on pipeline media, pressure class, and matching flange type.
Q4. What are typical maintenance cycles for blind flange assemblies?
Regular visual inspection and bolt re-torque every 12–36 months; hydrotest as per project code (API 598, EN 12266-1). Properly selected blind flange types should provide over 25 years service life without major overhaul.
Q5. Can blind flanges be custom-drilled for instrumentation or venting?
Yes. Custom machining is available for threaded (NPT, BSP), tapped, or integrally-welded nozzles—ideal for sampling, pressure relief/vent.
Q6. What is the typical delivery lead time and how is quality controlled?
Stock items: 3–7 days; standard production: 10–25 days. Each batch is subject to spectral PMI, ultrasonic/magnetic NDT, dimension checks per drawing, and is shipped with MTC and third-party inspection if required.
Q7. What warranty and after-sales support are provided?
Most manufacturers offer 5–10 year warranty (material and manufacturing defects), with ongoing technical support, rapid spares dispatch, and 24/7 online assistance for global projects.
9. Quality Control, Delivery & Service Commitment
- Inspection: Each lot is NDE-inspected, marked per ISO/EN/ASME/ASTM. Full batch traceability and PMI as standard.
- Test Records: Dimensional reports, hydrostatic/air leakage tests, and mechanical property certificates delivered with each shipment.
- Delivery Timeline: Standard sizes 3–7 days; specials/custom 10–25 days based on complexity.
- Documentation: Comprehensive records: EN 10204 3.1/3.2, PED, SGS, Lloyd's/DNV–GL as required.
- Warranty: 5–10 years (manufacturer dependent), covers leakage, corrosion, and dimensional conformity.
- After-Sales Support: 24/7 engineering assistance, installation guides, on-site support (where applicable).
10. Conclusion: Why Choose the Right Blind Flange Types?
The correct blind flange types selection ensures safe, efficient, and cost-effective plant operations—particularly for high-risk industries such as oil & gas, power, and chemicals. Partnering with an industry-certified supplier (see product details) guarantees compliance with stringent codes like ASME B16.5/47, API 6A, ISO 9001, and offers tailored solutions for complex engineering environments. Always verify certifications, materials, and technical service capabilities for long-term peace of mind.
References & Further Reading: